精益化管理方法与关键步骤解读,在如今竞争激烈的商业环境中,组织不断努力寻求提高运营效率、减少浪费、增强生产力的方法。其中一个备受推崇的方法学就是精益化管理方法与关键步骤解读。这种方法旨在通过系统化的方式优化流程,消除非增值活动,并zui大化客户价值。它起源于丰田生产方式(TPS),如今已经被全球各行各业的组织广泛采纳。在本文中,我们将深入探讨精益化管理方法与关键步骤解读的基本原理、步骤和好处。
精益化管理方法与关键步骤解读:理解关键原则
原则一:明确价值
在实施精益化管理之前,明确客户的价值观非常重要。价值指的是直接有助于满足客户需求的活动或流程。通过了解客户价值,组织可以将精力集中在改进正确的领域,并消除浪费。
原则二:绘制价值流
一旦确定了价值,下一步是绘制价值流。价值流图是从供应商到客户的整个流程的可视化呈现。它有助于识别浪费、瓶颈和改进机会。通过分析价值流,组织可以了解物料、信息和活动的流动情况,从而优化整个流程。
原则三:创造流动
创造流动涉及设计能够实现产品或服务平稳连续运行的流程。该原则强调消除延误、返工和其他形式的浪费的重要性。通过优化流动性,组织可以缩短交货时间,提高客户满意度,并增加生产力。
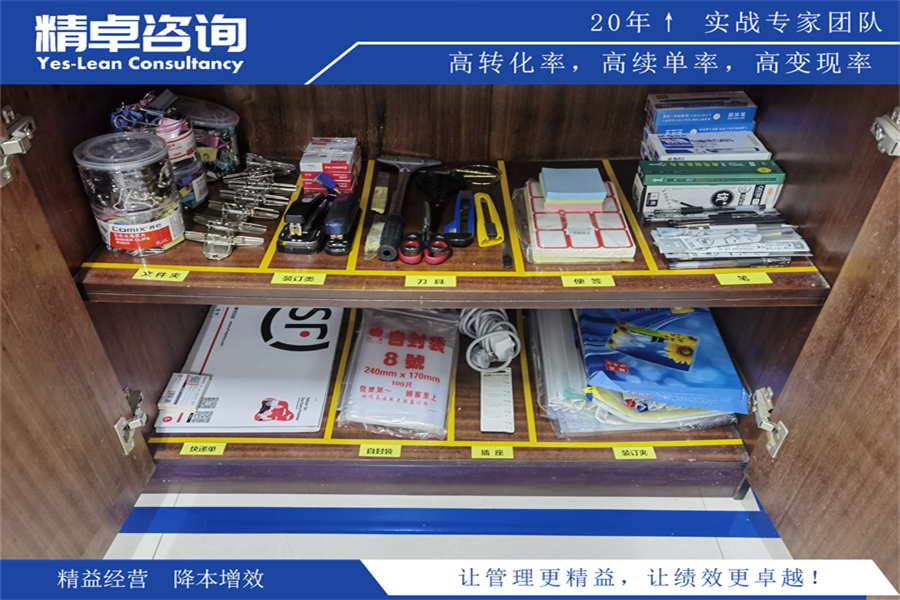
原则四:建立拉动
建立拉动意味着将生产或服务交付与客户需求相匹配。组织应该努力只在需要时生产所需数量的产品或提供服务。这有助于防止过度生产,减少库存成本,并提高对客户需求的响应能力。
原则五:追求卓越
追求卓越是持续改进流程和消除浪费的承诺。精益化管理鼓励建立持续改进的文化,让各级员工积极寻求改进的机会。该原则强调设定高标准、衡量绩效和持续推动改进。
实施精益化管理的关键步骤
步骤一:确定流程领域
实施精益化管理的第一步是确定需要改进的流程领域。组织应该分析其价值流,识别存在高浪费、低效率或客户不满意的流程。通过优先考虑这些领域,组织可以将努力集中在产生zui大影响的地方。
步骤二:员工参与
员工参与对于成功实施精益化管理至关重要。组织应该让各级员工参与过程改进的倡议。通过培养参与和赋权的文化,组织可以发挥员工集体知识和专业知识的作用。
步骤三:分析和改进
一旦确定了流程领域并获得员工的参与,就是时候进行分析和改进了。这包括绘制当前流程状态图,识别瓶颈和浪费,并设计改进后的未来状态。组织应该利用价值流图、根本原因分析和改善活动等工具来推动有意义的改进。
步骤四:实施和监控
实施和监控是确保持续改进的关键。组织应该执行计划的改进措施,密切监控关键绩效指标(KPI),并衡量变化的影响。定期审查和评估将有助于识别进一步的改进机会,并为未来的精益化倡议提供宝贵的见解。
常见问题解答
问题1:实施精益化管理有哪些关键好处?
精益化管理带来了许多好处,包括提高运营效率、减少浪费、增加生产力、提高客户满意度和节省成本。通过消除非增值活动和优化流程,组织可以实现更好的资源利用和持续改进的文化。
问题2:精益化管理能适用于非制造行业吗?
是的,精益化管理原则可以应用于制造业以外的各个行业。精益概念已经成功应用于医疗保健、物流、软件开发和服务型行业。关键是根据特定的背景和行业要求调整原则和工具。
问题3:如何保持通过精益化管理实现的改进效果?
要保持改进效果,需要长期致力于持续改进。组织应该建立绩效指标,定期审查进展,并为员工提供持续的培训和支持。此外,培养鼓励员工参与、创新和解决问题的文化也有助于持续改进的实现。
问题4:精益化管理存在哪些风险或挑战?
尽管精益化管理带来了重要好处,但也存在一些挑战。一些常见的风险包括对改变的抵触、缺乏高层管理支持、不切实际的期望以及难以衡量无形改进的困难。然而,通过合理的规划、有效的变革管理和专注于建立精益文化,这些挑战是可以克服的。
问题5:有哪些行业领先的组织成功实施了精益化管理?
是的,有很多组织成功实施了精益化管理并取得了显著的成果。丰田是精益化原则的发起者,常常被引用为典型案例。其他一些成功采用精益化管理的知名公司包括通用电气、亚马逊和耐克。这些组织展示了精益原则在实现卓越运营和竞争优势方面的有效性。
问题6:如何在组织中开始精益化管理?
要开始精益化管理,建议寻求专家指导并利用现有资源。参与精益顾问或参加精益培训计划可以提供宝贵的见解和实际知识。此外,探索精益管理的案例研究、书籍和在线资源可以帮助建立坚实的理解基础。
精益生产不仅仅是很多的手法和工具,更重要的是一种思想传承,就像顾问说的那样,建立精益生产的DNA。那么,如何有效的推进精益生产?精益生产在推行过程中,应注意些什么问题而预防推行失败呢!下面总结一些国内推行的问题,给各位提供一些借鉴和帮助。推行成功的企业都是一样的,推行不成功的企业,各有各的不幸。
1、企业管理基础太差,草草上马。
企业连zui起码的5S或6S都没做好,现场管理混乱;中基层管理人员素质差,管理凭借经验,做事凭感觉;过程质量控制无效,只有处罚……如此的企业加入精益推行行列,肯定是吃败仗。做精益生产推行的企业,首先要求企业自身做好基本的现场管理、具有一定改善基础的能力。切忌,不明自己,草率上马。
2、导入精益生产前没有端正思想,导入前的期望与导入后的结果产生落差。
“冰冻三尺非一日之寒”,在中国推行精益生产需要有一个“汉化”的过程。日本丰田之所以在全球很出名,其生产制造模式使许多人膜拜和学习,这是经过60多年来不断持续改善和沉淀的结果。急功近利、急于求成的思想也使许多企业在精益管理推行中夭折。
企业管理者想快速把企业做好、做赚钱,思路本身是对的,选择精益管理也是非常正确的。但是,冲着“利”去,容易让企业管理者在推行过程中被个体效率诱惑而忽视了整体效率;只看到短期利益而忽视了长期利益;只看到企业的利益而忽视员工利益的共同成长与社会责任。
要明白精益不是神话,罗马不是一天建成的,对精益生产的导入与推行要有打持久战的打算,急切冒进的推进精益是不切实际的。要循序渐进地让大家了解精益变革对公司及个人带来的好处,减少激进式推进带来的阻力。
结论
精益化管理方法与关键步骤解读为组织优化流程、消除浪费和提高运营效率提供了强大的框架。通过采纳识别价值、绘制价值流、创造流动、建立拉动和追求卓越的关键原则,组织可以实现可持续的改进,并为客户创造更大的价值。
尽管迈向精益卓越的过程可能存在挑战,但所获得的好处是值得努力的。通过员工参与、运用精益工具和营造持续改进的文化,组织可以释放出其全部潜力,并在当今不断变化的商业环境中保持竞争优势。