7S管理(整理、整顿、清扫、清洁、素养、安全、节约)是企业精益管理的核心工具,但许多企业面临“短期有效、长期失效”的困境。作为专业精益顾问,我将结合行业实践与数据,系统解析如何通过机制设计、文化渗透和持续改进实现7S管理的长效化。以下是四大关键策略:
一、建立长效保障机制:固化标准与动态监督
标准化操作程序(SOP)制度化
制定可量化的7S执行标准,如“整顿三定原则”(定点、定容、定量)要求物品定位误差≤5cm,标识清晰度100%。
将标准嵌入岗位职责,例如仓库管理员每日需完成“清扫清单”并签字确认。
三级监督与闭环改进
基层自查:员工每日按《7S点检表》自查(如工具归位率、通道通畅度)。
中层周检:部门负责人每周核查,使用“红牌作战”标记问题区域(红牌整改率需达95%)。
高层评审:管理层季度审计,结合KPI(如事故率、空间周转率)调整标准。
数据化绩效管理
绑定7S指标与绩效考核:某制造企业将“清洁达标率”与奖金挂钩后,设备故障率下降40%。
数字化看板实时监控:通过IoT传感器监测通道占用率、库存阈值,自动触发预警。
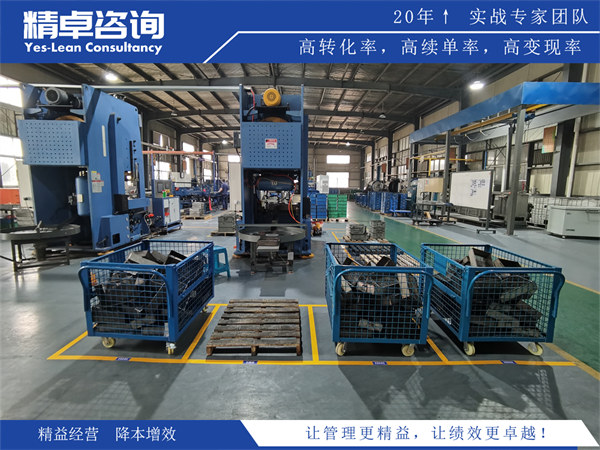
二、文化驱动:从被动执行到全员自觉
领导层示范与承诺
高管每月参与“7S实践日”(如车间清扫),并将7S纳入战略会议议题。
案例:某日企CEO因未通过安全区域检查主动扣薪,推动全员合规率升至98%。
员工赋能与荣誉体系
设立“改善提案积分制”:员工建议被采纳可兑换奖励(如某仓库年收提案200+条,节约成本189万元)。
评选“7S之星”并举办授勋仪式,增强参与感。
持续教育机制
新员工必修7S沉浸式培训(含VR安全演练);
每季度“7S知识竞赛”巩固认知,避免标准淡化。
三、工具与方法:科学维持动态优化
目视化管理升级
引入色标系统:红色(危险区)、黄色(过渡区)、绿色(安全区),实现“一眼管理”。
电子看板联动生产系统:实时显示设备清洁状态、物料周转速度。
持续改进技术应用
PDCA+5W1H循环:针对问题深度溯源(如用鱼骨图分析清洁滑坡原因)。
定点摄影法:同一角度拍摄改善前后对比,视觉化成果激励团队(某企业6个月通道宽度优化50%)。
标杆对标与外部赋能
每年参访行业标杆工厂,引入第三方审计(如日本JIPM认证)暴露盲点。
案例:某车企借力顾问重构仓库节约标准,空间利用率提升35%。
四、领导作用与资源保障:顶层设计决定长期性
资源倾斜:预算单列7S专项基金(占营收0.5%~1%),用于工具更新、奖励池。
组织保障:设立常设7S推进委员会,由副总直管,避免“运动式推行”。
风险预案:制定《7S滑坡应对手册》,明确流程异常时的快速响应机制。
结语:7S管理的本质是“文化韧性”
长期维持7S的核心在于将标准内化为组织习惯。丰田工厂数十年如一日的高标准,源于其“素养”环节对行为惯性的塑造。建议企业以“三年为周期”分阶段深化:首年建机制、次年强文化、三年成生态。立即行动点:今日起建立“7S日历”,每日记录一项微小改进,365天后将见证文化质变。