在生产车间实施
5S管理能够提高生产效率、安全性和员工满意度。下面将详细解释生产车间5S管理制度的建立步骤和运行机制:
1.生产车间5S管理制度建立步骤
1.Seiri(整理):
-确定目标:明确整理的范围和目标,如清理工作台、仓库等。
-分类物品:将物品分为必要和不必要的两类,清除不必要物品。
-建立标准:制定整理标准和操作流程,保持整理效果。
2.Seiton(整顺):
-规划工位:设计合理的工作布局,确保物料和工具摆放有序。
-标示物品:使用标识、标牌等方式标明物品摆放位置,方便取放、归还。
3.Seiso(清扫):
-制定清洁计划:安排清洁任务和频率,确保设备和环境整洁。
-培训员工:对员工进行清洁的方法和标准操作培训,提高清洁意识。
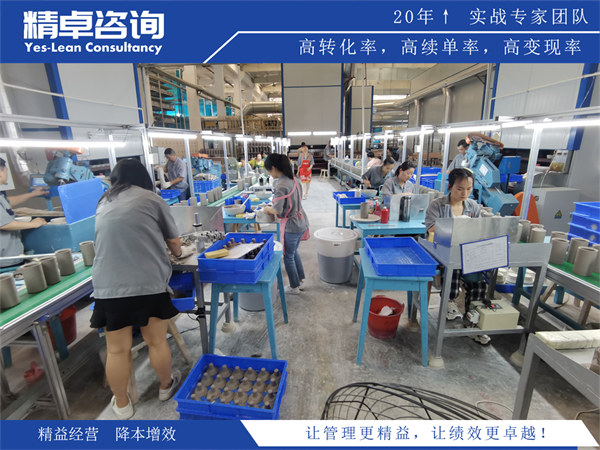
4.Seiketsu(清洁):
-建立标准:建立清洁检查标准和评估机制,确保每日清洁工作。
-持续改进:定期评估清洁效果,发现问题并改进清洁标准。
5.Shitsuke(躬行):
-建立监督机制:建立巡视、督导机制,确保各项5S管理落实到位。
-奖惩机制:建立奖励制度激励员工参与5S管理,也对违反规定进行惩罚。
2.生产车间5S管理运行机制
1.定期检查:设立定期检查计划,检查5S执行情况,找出问题并及时整改。
2.持续培训:定期为员工提供5S管理方面的培训,提高其执行力和质量意识。
3.奖惩激励:建立奖惩机制,激励员工积极参与5S管理,形成持续改进的氛围。
4.改进计划:基于定期检查结果,制定改进计划和措施,持续提升5S管理水平。
5.持续改进:鼓励员工提出改进建议,推动5S管理不断优化和完善。
通过严格执行生产车间5S管理制度的建立步骤和运行机制,企业可以提高生产效率、质量,降低事故发生率,营造整洁有序的生产环境,从而提升竞争力和员工满意度。