5S原则是一种管理方法,通过整顿(Sort)、整理(Setinorder)、清扫(Shine)、标准化(Standardize)和维持纪律(Sustain)这五个步骤,提高工作环境的效率、安全性和舒适度。以下是对5S原则的简介以及在生产现场实际运用的指南:
1.整顿(Sort)
概念:剔除不必要物品,优化工作空间。
实际运用指南:
-审查生产现场,识别并分类必需与非必需物品。
-清除不需要的物品,确保只有必要设备和材料存放在工作区域。
-设立明确的储存位置,避免混乱堆积。
2.整理(Setinorder)
概念:确定每样物品固定位置,提高操作效率。
实际运用指南:
-标示每种物品的存放位置,并确保易于识别。
-制定统一的归纳规则和储藏方案。
-减少寻找时间,提高操作效率。
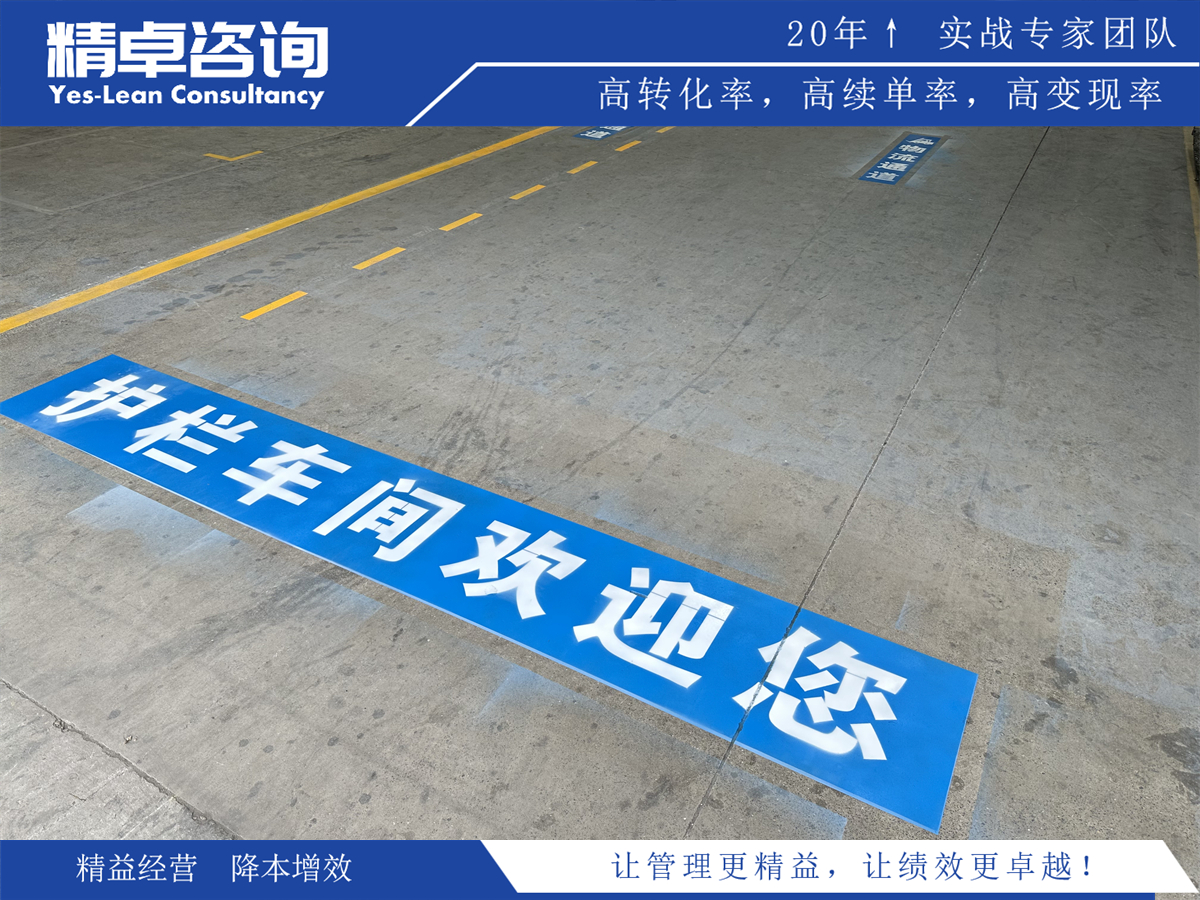
3.清扫(Shine)
概念:维持工作环境清洁整洁。
实际运用指南:
-制定清洁计划和责任分配表。
-进行日常清洁工作,并定期进行大扫除。
-提高员工对清洁卫生重要性的认识。
4.标准化(Standardize)
概念:建立6S管理体系,确保标准执行任务。
实际运用指南:
-制定操作标准和程序规范文件。
-培训员工如何执行各项6S活动。
-定期审查并更新标准操作程序。
5.维持纪律(Sustain)
概念:巩固前四个S,并使之成为组织文化一部分。
实际运用指南:
-鼓励员工自我监督与互相监督,形成良好习惯。
-设立奖惩机制促使员工积极参与6S活动。
-持续改进,并将6S融入企业文化中。
通过贯彻落实5S原则,在生产现场可以优化生产流程、提升效率、增强安全性,并形成良好的企业文化。建议在引导员工学习并应用5S原则时注重培训、跟踪执行情况并进行反馈调整,在持续改进中不断完善管理体系。