什么是5S原则及其在工厂管理中的实际应用
5S原则是一种源自日本的管理方法,旨在通过整顿、整理、清扫、标准化和维持纪律这五个步骤,提高工作场所的效率、安全性和舒适度。下面将详细介绍5S原则以及其在工厂管理中的实际应用:
1.整顿(Seiri-Sort)
概念:在整顿阶段,目标是识别并清除不必要的物品,只保留必需的设备、工具和材料。
实际应用:
-识别并分类存放物品,区分出必需与非必需物品。
-清除无用物品,避免杂乱堆积影响生产流程。
-建立合理储存系统,确保员工能够快速找到需要使用的物品。
2.整理(Seiton-SetinOrder)
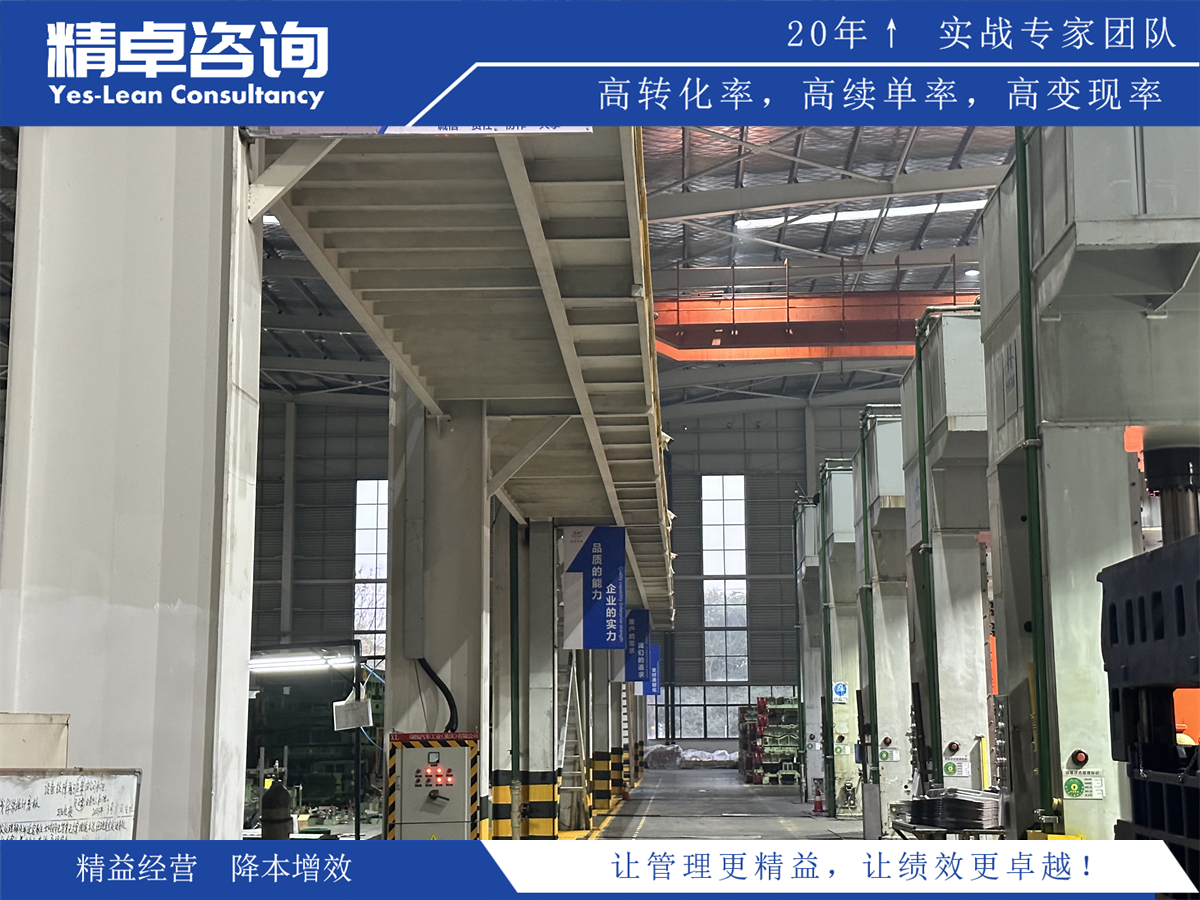
概念:整理阶段旨在建立明确的存放位置,并确保所有物品有固定归位处。
实际应用:
-设立每样物品固定位置,并标示清晰。
-制定标准化分类规则和储存方案。
-提高操作效率,减少寻找时间。
3.清扫(Seiso-Shine)
概念:清扫不仅是简单地打扫卫生,更重要的是培养员工对于干净环境的意识。
实际应用:
-制定清洁计划和责任分配表。
-定期进行大扫除,保持车间环境整洁。
-增强员工参与感,并培养对清洁卫生的重视。
4.标准化(Seiketsu-Standardize)
概念:标准化阶段主要是建立6S管理体系,并确保所有员工都按照相同标准执行任务。
实际应用:
-确定6S执行标准和程序规范。
-培训员工如何执行各项6S活动。
-定期审查并更新标准操作程序。
5.维持纪律(Shitsuke-Sustain)
概念:维持纪律是指通过教育培训和自我监督来巩固前四个S,并使之成为组织文化的一部分。
实际应用:
-鼓励员工自我监督与互相监督,形成良好习惯。
-奖惩机制鼓励员工积极参与6S活动。
-持续改进,并将6S作为长期发展战略一部分。
结论:
通过有效贯彻5S原则,在工厂管理中可以提高生产效率、优化生产流程、增强安全性、节约时间成本等多方面带来益处。这一方法不仅能改善现有情况,还可以塑造出一个有序且高效运转的企业环境。