在生产现场实施6S管理是提高生产效率、优化工作环境、降低浪费的重要手段。下面将详细介绍生产现场6S管理的实施步骤,并结合成功案例进行深入分析:
实施步骤:
1.第一S-整顿(Sort):
-识别并清除不必要的物品,确保工作区域没有过多杂物干扰生产流程。
2.第二S-整理(Setinorder):
-设定标准化的物品摆放位置,通过标识和归类使得员工易于找到所需物品。
3.第三S-清扫(Shine):
-定期清洁设备和工作区域,保持整洁有序,提高生产效率并延长设备寿命。
4.第四S-标准化(Standardize):
-制定操作流程和标准规范,确保所有员工按照相同标准执行工作。
5.第五S-培养纪律(Sustain):
-建立持续改进机制和监控体系,持续推动团队保持良好习惯和纪律性。
6.第六S-自律(Safety):
-强调安全意识和行为规范,确保员工安全与健康,防止事故发生。
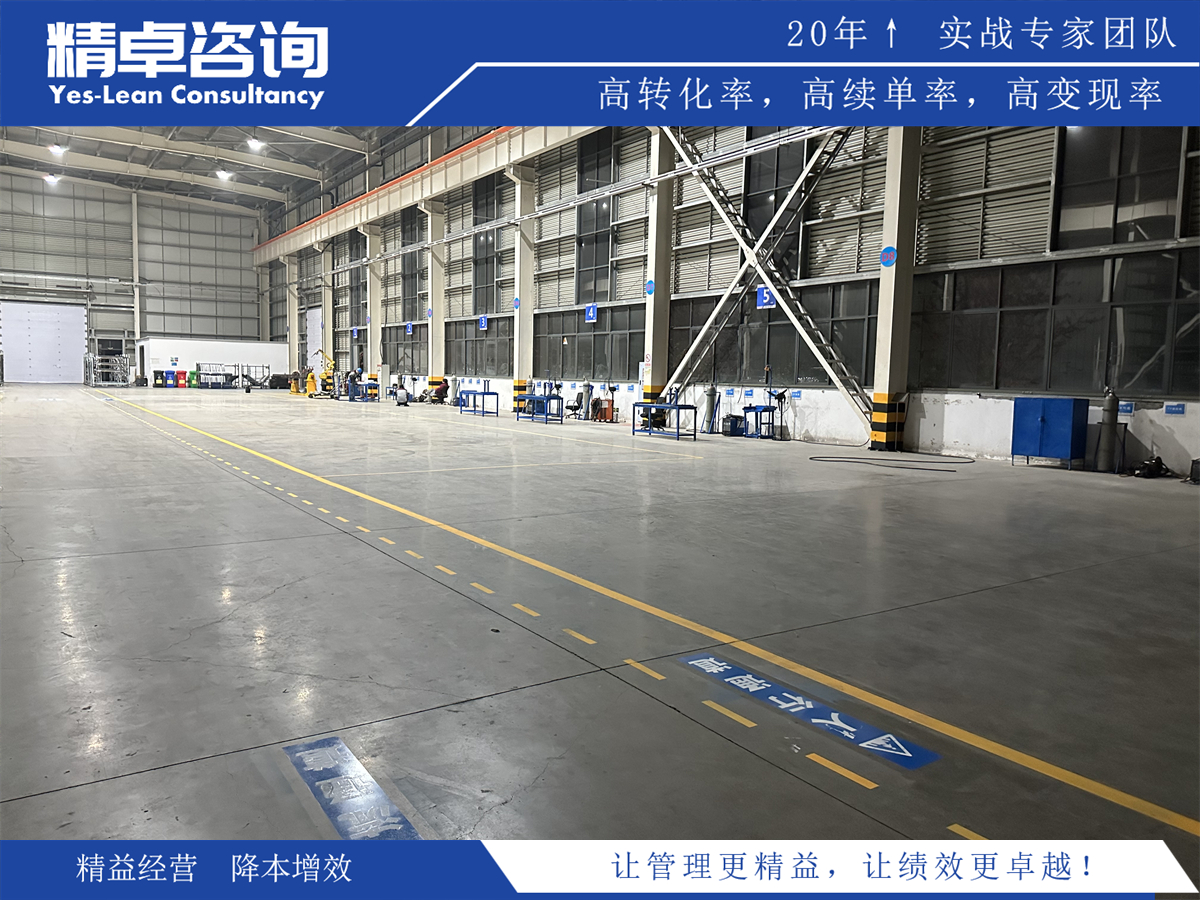
成功案例分析:
公司名称:ABC制造公司
-挑战:ABC公司在生产车间存在着杂乱无章、浪费严重等问题,导致生产效率低下。
-解决方案:ABC公司引入了6S管理,并严格执行以下步骤:
1.对各部门进行整顿评估清理不必要物品。
2.设立统一的标准化摆放位置,并对每个岗位进行指导。
3.每日定时清扫车间以保持整洁。
4.制定操作规范文件并进行培训普及。
5.设立奖励机制激励员工遵守规则。
6.加强安全意识培训并设置紧急预案。
-成果:经过6个月的实施,在ABC公司内部形成了良好的5S文化氛围:
生产效率提高了15%;
错误率降低了20%;
员工满意度明显提升;
这个案例表明了通过严格执行6S管理步骤,并结合适当奖励机制与培训计划,在企业内部可以取得显著的改善与成果。通过此种方式建立起来的5S文化能够帮助企业提高竞争力与市场份额。