车间6S现场管理是提高生产效率、优化工作环境、降低错误率的重要手段。为了持续改进管理水平,需要对实施效果进行评估并采取相应的改进措施。以下是对车间6S现场管理实施效果评估及持续改进方法的探讨:
实施效果评估方法:
1.生产效率提升
-指标:生产周期缩短、生产线稳定性提高等。
-评估方法:比较实施6S前后的生产数据,如产量、产能利用率等指标,观察是否有明显提升。
2.员工满意度调查
-指标:员工参与度、工作舒适度等。
-评估方法:定期进行员工满意度调查或面谈,收集员工反馈和建议,了解他们对6S管理的看法和体验。
3.错误率降低
-指标:产品次品率、质量事故频率等。
-评估方法:分析质量数据变化,检视错误类型和频率是否有所降低,以验证6S对质量影响的有效性。
4.安全记录
-指标:安全事故发生率、安全违规次数等。
-评估方法:记录安全事件发生情况,分析原因并制定改进措施,确保车间安全管理得到有效执行。
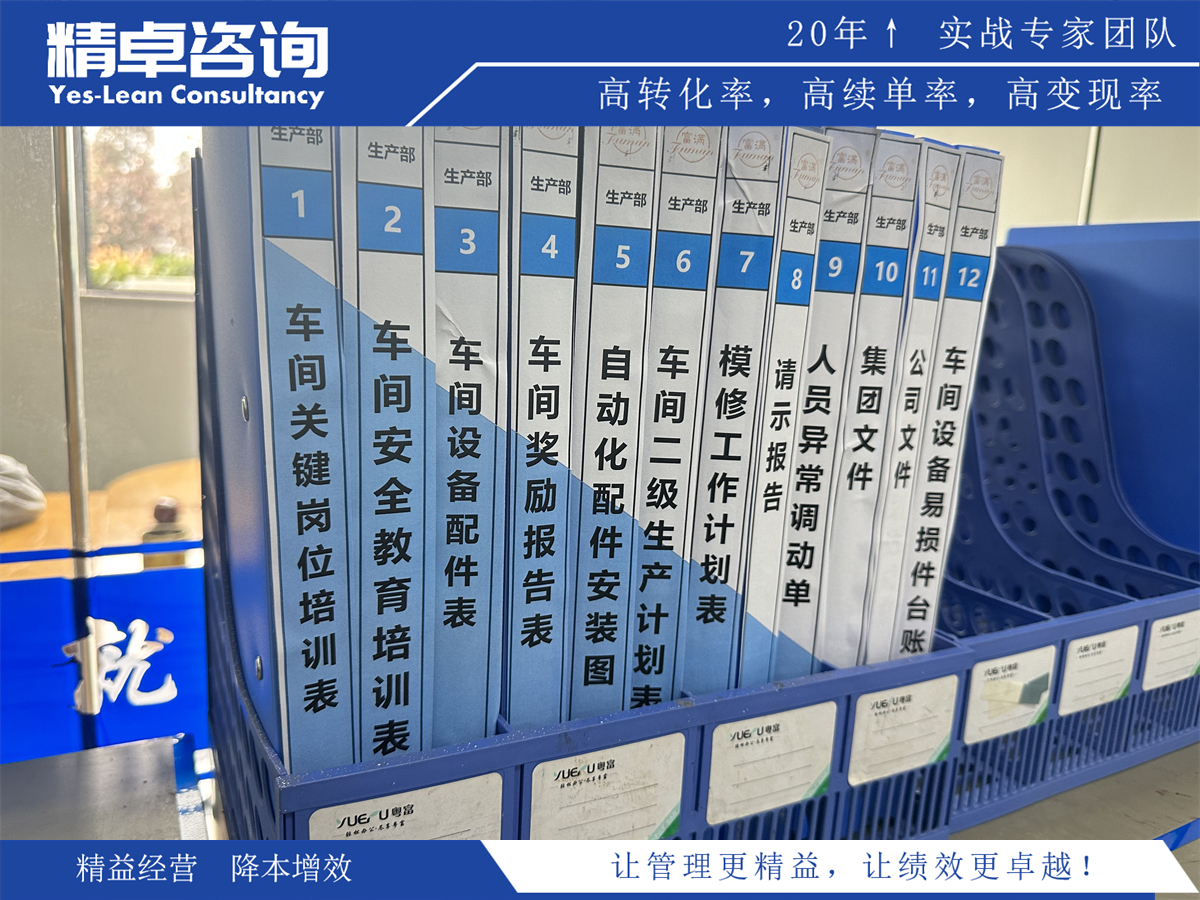
持续改进方法:
1.定期评估
-建立定期的6S管理评估机制,包括审核车间现场情况、与员工交流反馈,并根据评估结果制定改进计划。
2.持续培训
-组织针对不同岗位人员的培训课程,提升员工对6S管理的理解和执行能力,促进文化落地和持续推动。
3.奖励机制
-设立奖励机制激励员工参与6S管理活动,并表彰优秀个人或团队,在激励中推动良好行为养成。
4.问题解决机制
-建立问题反馈渠道和迅速解决机制,鼓励员工报告问题并及时处理,确保问题不断暴露和解决。
通过以上实施效果评估和持续改进方法的运用,车间可以不断优化6S现场管理模式,在提高生产效率、促进员工参与度、降低错误率等方面取得更加显著的成效,并在竞争激烈的市场中保持领先地位。