在工业管理中,7S现场管理是对传统6S模型的扩展,加入了安全(Safety)这一层面,以更全面地提升工作场所的管理和效率。下面是7S现场管理的实施步骤和效益评估方法的解析:
1.7S实施步骤:
a.Sort(整理):
-确定哪些物品是必要的,清除多余的物品。
-创建有效的库存管理系统,减少浪费和过剩物品。
b.Setinorder(整顿):
-设立物品归位标准,确保每样物品都有固定的位置。
-设计清晰的工作场所布局,减少搜寻和移动时间。
c.Shine(清扫):
-持续清洁工作场所,确保设备和设施保持良好状态。
-建立清洁检查标准,保持整体环境干净整洁。
d.Standardize(标准化):
-制定标准操作程序,确保每个任务都有明确的步骤和标准。
-建立规范文件管理系统,确保信息和文件易于访问。
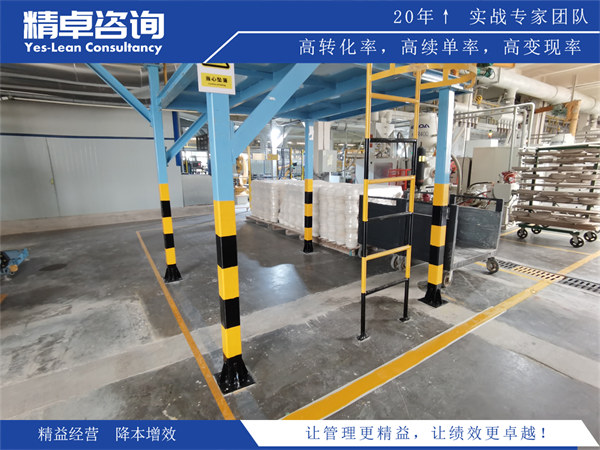
e.Sustain(培训):
-提供员工培训,使员工能够理解和遵循7S标准。
-建立持续改进文化,鼓励员工参与改进和提出建议。
f.Safety(安全):
-强调工作场所安全标准,确保员工在工作中安全。
-实施安全培训和意识提升活动,提高员工对安全的重视。
g.Standardize(制度化):
-制定并遵守规章制度,确保7S管理的长期有效性。
-定期评估和审查制度,不断优化和改善管理方法。
2.效益评估方法:
a.关键绩效指标(KPI):
-建立和追踪关键绩效指标,如工作效率、产量、质量等。
-根据KPI数据评估7S实施效果,及时发现问题并进行改进。
b.员工满意度调查:
-定期进行员工满意度调查,了解员工对7S管理措施的看法。
-根据反馈意见调整管理方法,提高员工参与度和满意度。
c.安全记录:
-统计安全事故发生情况和报告,评估安全管理水平。
-持续改进安全措施,确保工作场所的安全。
d.生产效率分析:
-分析工作场所的生产效率和流程优化情况。
-比较实施7S前后的生产效率变化,评估管理效果。
e.质量控制:
-定期进行质量控制和检查,评估产品和服务质量。
-评估7S管理对质量控制的影响,持续改进质量水平。
结论:
通过严格执行7S现场管理的实施步骤,并采用有效的效益评估方法,可以提升工作场所的整体效率、安全性和员工满意度。定期跟踪关键绩效指标、评估安全记录、分析生产效率和质量控制,将有助于持续改进管理水平,确保7S管理效果最大化。